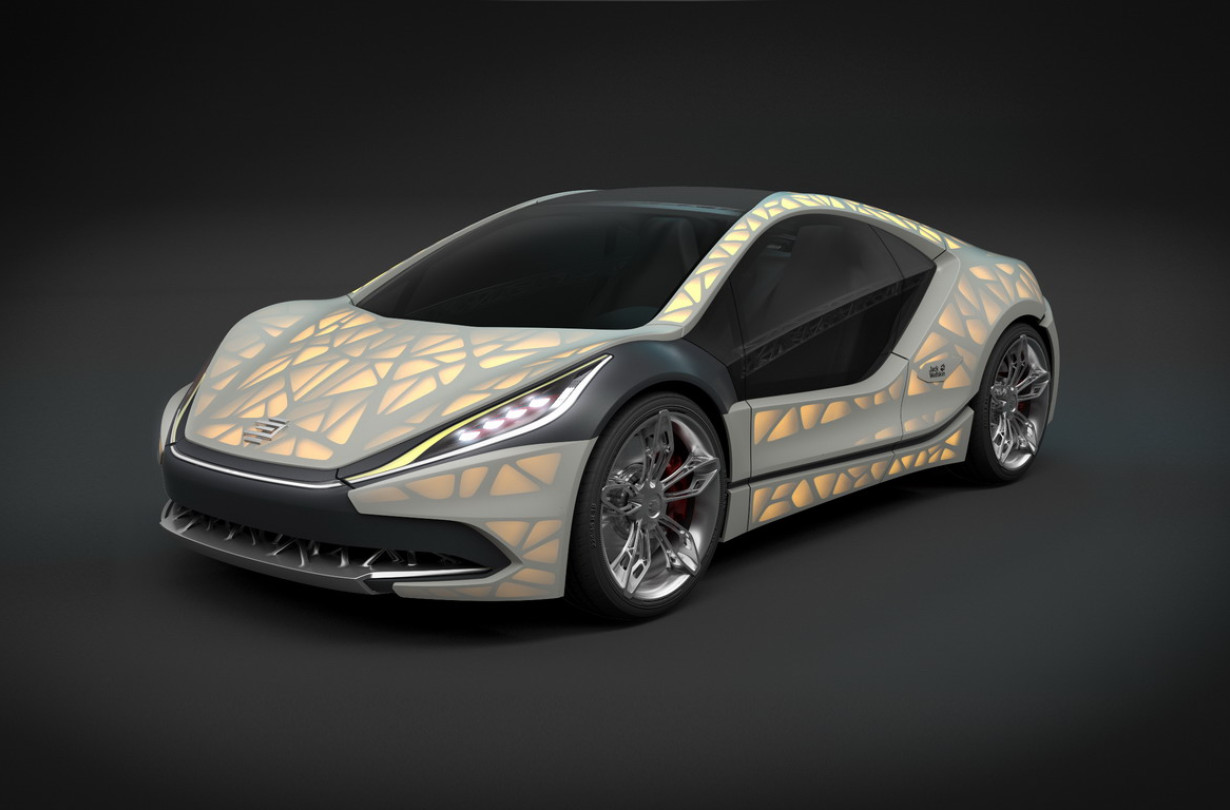
EDAG Light Cocoon: η αβάσταχτη ελαφρότητα
Το πρωτότυπο Light Cocoon της EDAG έχει εξωτερικό αμάξωμα από ύφασμα, ενώ τα βασικά του εξαρτήματα είναι κατασκευασμένα με 3D printing.
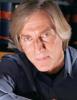
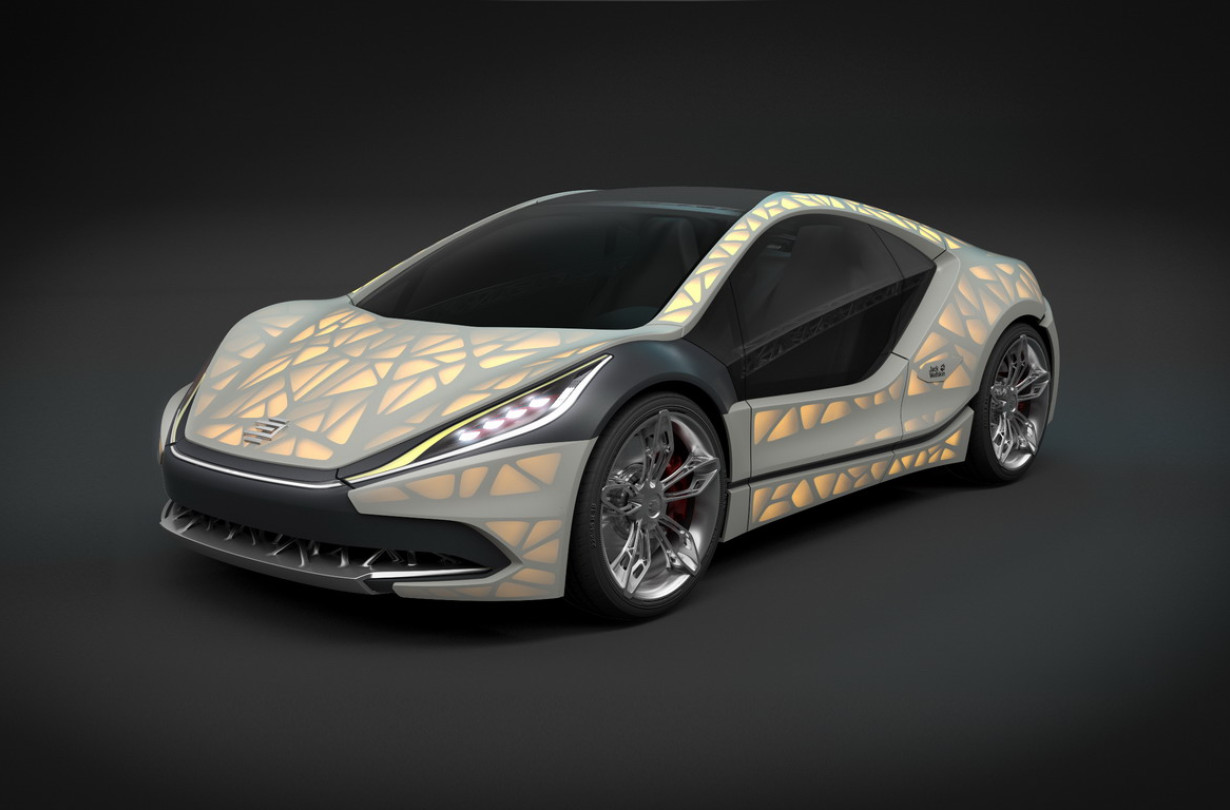
Η εξοικονόμηση βάρους είναι σήμερα κορυφαία προτεραιότητα για την αυτοκινητοβιομηχανία, ώστε να μειωθεί η κατανάλωση και να αυξηθεί η αυτονομία των ηλεκτρικών αυτοκινήτων. Όμως η εξοικονόμηση αυτή, με τη χρήση συμβατικών μεθόδων και υλικών, γίνεται ολοένα πιο δύσκολη και ακριβή.
Η εξειδικευμένη γερμανική φίρμα EDAG Engineering ισχυρίζεται ότι έχει εξελίξει μια επαναστατική μέθοδο κατασκευής πανάλαφρων αυτοκινήτων αντί κλάσματος του κόστους. Η μέθοδος αυτή συνδυάζει νέες τεχνολογίες, όπως η μεγάλης κλίμακας τρισδιάστατη εκτύπωση (3D printing) για τα εξαρτήματα και η δημιουργία ενός πολύ ανθεκτικού, εύκαμπτου υφάσματος παντός καιρού για το εξωτερικό του αμαξώματος.
Η φίρμα εξέθεσε τη δουλειά της στο πρόσφατο Σαλόνι της Γενεύης, σε ένα πρωτότυπο που ονόμασε EDAG Light Cocoon. Αυτή η νέα διαδικασία έχει τη δυνατότητα όχι μόνο να κατασκευάσει ελαφρύτερα αυτοκίνητα, αλλά επίσης να εξοικονομήσει μεγάλο μέρος από το αρχικό κόστος για τους κατασκευαστές, μειώνοντας σημαντικά και το χρόνο εξέλιξης των νέων μοντέλων.
Η μέθοδος 3D printing, γνωστή επίσης και ως «προσθετική κατασκευή», κάνει ένα τρισδιάστατο μοντέλο CAD (σχεδίασης με τη βοήθεια υπολογιστή) πραγματικότητα. Η μέθοδος παίρνει διάφορες μορφές. Το Light Cocoon είναι κατασκευασμένο με Στερεολιθογραφία (SLA), όπου υπεριώδεις ακτίνες λέιζερ στερεοποιούν ρητίνη σε αλλεπάλληλες πολύ λεπτές στρώσεις μέχρι να κατασκευαστεί το πλήρες αντικείμενο. Μεταλλικά αντικείμενα κατασκευάζονται με μία παρόμοια διαδικασία που ονομάζεται Selective Laser Sintering (SLS), όπου τη θέση της ρητίνης παίρνει μεταλλική σκόνη.
Για βιομηχανική χρήση, τα «εκτυπώσιμα» σε 3D μέταλλα, με τη μέθοδο SLS, περιλαμβάνουν τον χάλυβα, το τιτάνιο, το αλουμίνιο και τον χαλκό. Διαμορφωμένο από τη σκόνη, το τελικό προϊόν «είναι σχεδόν εξίσου ισχυρό όσο το βασικό υλικό», λέει ο Martin Hillebrecht, επικεφαλής του κέντρου ελαφριάς σχεδίασης της EDAG. «Μπορεί να συγκολληθεί και αντέχει σε κόπωση». Προβλέπει επίσης την πιθανότητα κατασκευής πλαστικών ενισχυμένων με ίνες.
Αν εφαρμοστεί σε ολόκληρο αυτοκίνητο, η προσθετική κατασκευή μπορεί να χρησιμοποιηθεί για τη δημιουργία μιας σύγχρονης μορφής δικτυώματος, με επιδράσεις από τη Φύση. Το ευαίσθητο στην όψη αλλά άκαμπτο πλαίσιο-χωροδικτύωμα του Light Cocoon θυμίζει τον σκελετό ενός φύλλου, ενώ τα πλευρικά στοιχεία που είναι ορατά κάτω από το ύφασμα μοιάζουν με την εσωτερική δομή των οστών ενός πουλιού.
Υφασμάτινο κάλυμμα; Το Light Cocoon είναι ντυμένο με ένα ειδικά εξελιγμένο, υψηλής αντοχής, παντός καιρού ύφασμα, που έχει φτιαχτεί από τη φίρμα outdoor ρούχων και εξοπλισμού Wolfskin. To “Light” είναι λογοπαίγνιο, καθώς το πρωτότυπο, όχι μόνο ζυγίζει πολύ λιγότερο από ένα ατσάλινο ή αλουμινένιο αυτοκίνητο, αλλά μπορεί και να φωτιστεί εσωτερικά με λυχνίες LED. Η εικονική αυτή «βαφή» σημαίνει ότι ο ιδιοκτήτης μπορεί να αλλάζει το χρώμα του αυτοκινήτου κατά βούληση, μέσω μιας οθόνης αφής ή μιας εφαρμογής σε smartphone.
Ένα υφασμάτινο κάλυμμα θεωρείται ευαίσθητο και επιρρεπές σε ζημιές από χτυπήματα και βανδαλισμούς, όμως η EDAG λέει ότι δεν είναι πιο ευπαθές από τη σκεπή ενός κάμπριο ή από το βαμμένο ατσάλινο ή αλουμινένιο αμάξωμα, ενώ επισκευάζεται αλλάζοντας κομμάτια του με νέα. Το ύφασμα πλένεται και το πρωτότυπο στη Γενεύη είχε οδηγίες πλυσίματος όπως οποιοδήποτε ρούχο.
Το ύφασμα είναι και εύκαμπτο. Τόσο εύκαμπτο που επιτρέπει στη δομή του αυτοκινήτου από κάτω να αλλάζει σχήμα. Ένα ρυθμιζόμενο σπόιλερ μπορεί να εκτείνεται χωρίς να αφήνει κενά, καθώς το ύφασμα τεντώνει για να καλύψει τη μεταβολή. Η ιδέα αυτή μπορεί εύκολα να εφαρμοστεί για να αλλάζει το όλο σχήμα του αυτοκινήτου, δίνοντας στον ιδιοκτήτη τη δυνατότητα να μεταβάλλει το στιλ και το χρώμα όπως και όποτε θέλει.
Η ιδέα ακούγεται φανταστική, αλλά η EDAG λέει ότι βασίζεται στην πραγματικότητα και είναι ζήτημα χρόνου το πότε η προσθετική κατασκευή με λέιζερ θα αναπτυχθεί για να επιτελέσει αυτό το σκοπό. Ήδη κατασκευάζονται με αυτόν τον τρόπο εξαρτήματα για την αεροδιαστημική βιομηχανία, αν και το μέγεθός τους είναι περιορισμένο. «Οι εργαλειομηχανές έχουν μεγαλώσει από τα 350 mm στα 650 mm σε δύο μόλις χρόνια», εξηγεί ο Hillebrecht. Και η τάση συνεχίζεται. Η EDAG πιστεύει ότι μεγαλύτερα τμήματα του εσωτερικού, όπως πίνακες οργάνων, θα μπορούν να γίνουν πραγματικότητα μέσα σε πέντε χρόνια, ενώ ολόκληρα αυτοκίνητα θα μπορούν να κατασκευαστούν με αυτή τη μέθοδο σε μια εικοσαετία.
Ένα μειονέκτημα είναι ο χρόνος που απαιτείται για τη διαδικασία της «εκτύπωσης», αλλά μέσα στα επόμενα 10 χρόνια, συνεχίζει ο Hillebrecht, «περιμένουμε να αυξηθεί η ταχύτητα κατά 100%». Η δυνητική οικονομία για τους κατασκευαστές αυτοκινήτων που θα υιοθετήσουν αυτή την τεχνολογία, αν γίνει πραγματικότητα σε μεγάλη κλίμακα, θα είναι πολύ σημαντική.
Για να εγκαταστήσουν συμβατικές υποδομές παραγωγής ενός νέου μοντέλου σήμερα, οι κατασκευαστές πρέπει να επενδύσουν εκατομμύρια σε εργαλειομηχανές και εργαλεία. Σε πρέσες και καλούπια πρεσών. Με τη νέα μέθοδο, η διαμόρφωση αμαξωμάτων σε πρέσες θα ανήκει πλέον στο παρελθόν, όπως και τα αντίστοιχα καλούπια. Όσο για την επεξεργασία κοπής, «μια μηχανή προσθετικής με λέιζερ μπορεί να αντικαταστήσει 17 τόρνους, δράπανα και φρέζες», λέει ο Hillebrecht.
Η ίδια μηχανή θα μπορεί να παράγει οποιοδήποτε σχήμα και στιλ αμαξώματος χωρίς αλλαγή εργαλείων, μόνο με την αλλαγή του αρχείου CAD στον υπολογιστή ελέγχου. Αναμένεται οι πρώτες εφαρμογές σε ολόκληρο αμάξωμα να γίνουν από κατασκευαστές μικρού όγκου παραγωγής «όπου η επένδυση σε εργαλεία κατασκευής αποτελεί μια σοβαρή απόφαση».
Η προσθετική κατασκευή θα επιτρέπει ολόκληρη η δομή του αμαξώματος να παράγεται με μία μόνη διαδικασία, ενώ τα άλλα εξαρτήματα θα φτιάχνονται ξεχωριστά. Άλλες δυσκολίες θα είναι η αντιμετώπιση του NVH (θορύβων και κραδασμών), αλλά ο Hillebrecht λέει ότι ισχύουν οι ίδιοι κανόνες για την μόνωση της καμπίνας επιβατών με αυτούς που ισχύουν για άλλα υλικά. Κατά την EDAG, υπήρξε μεγάλο ενδιαφέρον για την ιδέα από αυτοκινητοβιομηχανίες, και ειδικά στο συνέδριο Inside 3D Printing, που έγινε αυτό το μήνα στο Βερολίνο.
«Φαίνεται πως όλοι οι κατασκευαστές αυτοκινήτων αντιπροσωπεύονταν στο συνέδριο», σημειώνει ο Hillebrecht. «Πιστεύω πως οι βιομηχανικές εφαρμογές ακολουθούν την καταναλωτική αγορά, οπότε αυτό δεν είναι απλά προϊόν υπερβολικής προβολής. Είναι μια αληθινή βιομηχανική επανάσταση».