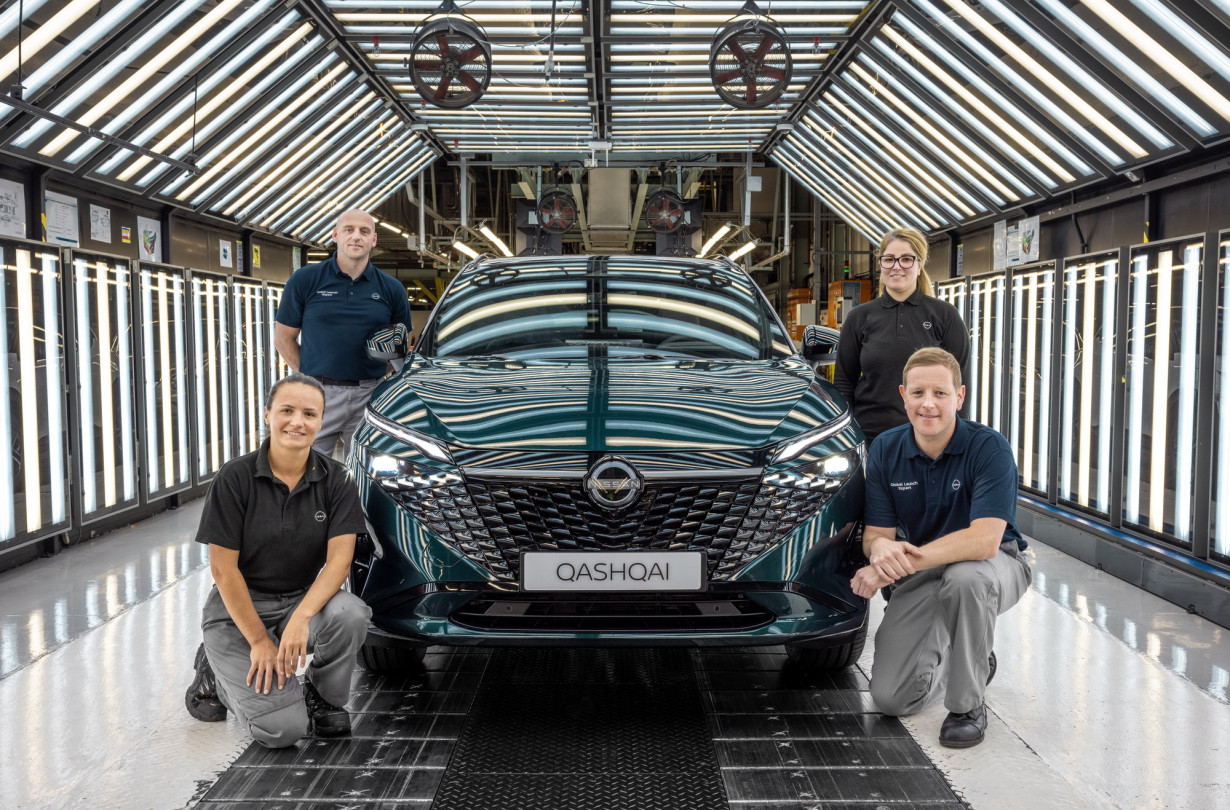
Αποστολή στο νέο, βιώσιμο εργοστάσιο της Nissan στο Sunderland
Στo ανανεωμένo Nissan Motor Manufacturing UK όπου κατασκευάζεται το νέο Qashqai, 19.000 ηλιακοί συλλέκτες και οι δέκα ανεμογεννήτριες παράγουν το 20% των αναγκών του εργοστασίου σε ηλεκτρική ενέργεια. Με το «EV36Zero» να προβλέπει να φτάσει στο 100%.
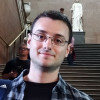
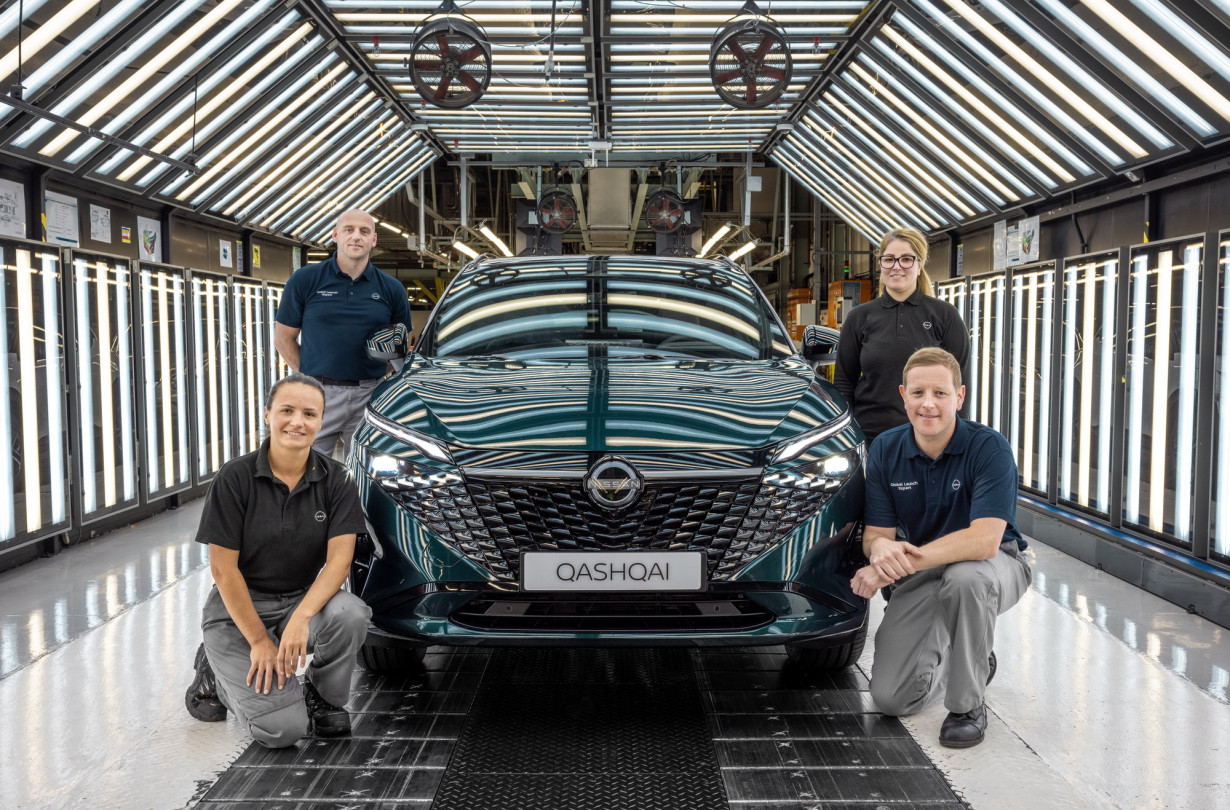
Συχνά γράφεται στον αυτοκινητικό -και όχι μόνο- Tύπο για τις νέες μεθόδους παραγωγής που ακολουθούν οι μεγάλες αυτοκινητοβιομηχανίες. Εμείς θέτουμε τον δάκτυλον επί τον τύπον των ήλων στο ανακαινισμένο και εκσυγχρονισμένο εργοστάσιο της Nissan στο Sunderland.
Οι νέες τεχνικές που εφαρμόζουν οι αυτοκινητοβιομηχανίες προφανώς και έχουν στόχο την ταχύτερη και αποδοτικότερη κατασκευή στα όλο και πιο σύνθετα και πολύπλοκα αυτοκίνητα που επιβάλλουν οι σύγχρονες συνθήκες και απαιτήσεις. Tόσο από θέμα σχεδίασης του αμαξώματος και των γραμμών που το σχηματίζουν όσο και της τεχνολογίας που τα σύγχρονα αυτοκίνητα ενσωματώνουν προς βοήθεια του οδηγού, της άνεσης των επιβατών και της ασφάλειας όλων των χρηστών του δρόμου.
Ο ανθρώπινος παράγοντας είναι στρατηγικά ενσωματωμένος στην παραγωγή του Sunderland, σε σημεία μάλιστα όπου άλλοι κατασκευαστές επιλέγουν την αυτοματοποίηση
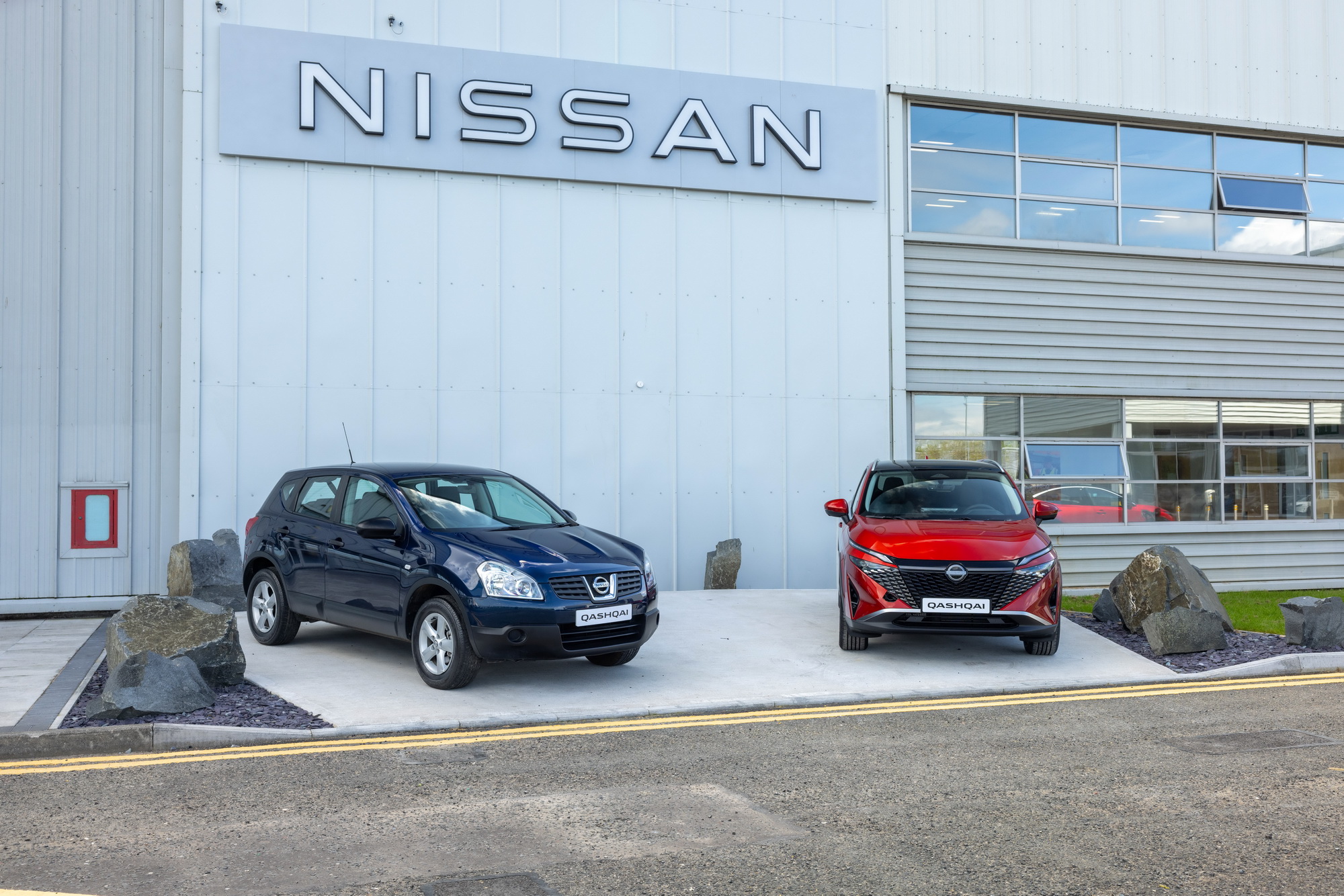
Τις περισσότερες φορές ωστόσο, το κοινό και οι δημοσιογράφοι μαθαίνουν για τέτοιου είδους εξελίξεις είτε από δελτία τύπου είτε από συνεντεύξεις στελεχών της αυτοκινητοβιομηχανίας. Τουτέστιν, όλες οι συζητήσεις και αναφορές παραμένουν στη σφαίρα της μηχανολογικής και δημοσιογραφικής θεωρίας.
Με αφορμή την έναρξη παραγωγής της ολοκαίνουργιας, τελευταίας γενιάς του Qashqai, η Nissan προσκάλεσε μεταξύ άλλων και το DRIVE, να επισκεφθεί το εργοστάσιο παραγωγής στο Sunderland της Αγγλίας. Και να εξερευνήσει μέσα από τον δημοσιογραφικό φακό το σύνολο της γραμμής παραγωγής, τόσο του Qashqai όσο και του μικρότερου αδερφού Juke αλλά και του 100% ηλεκτρικού Leaf.
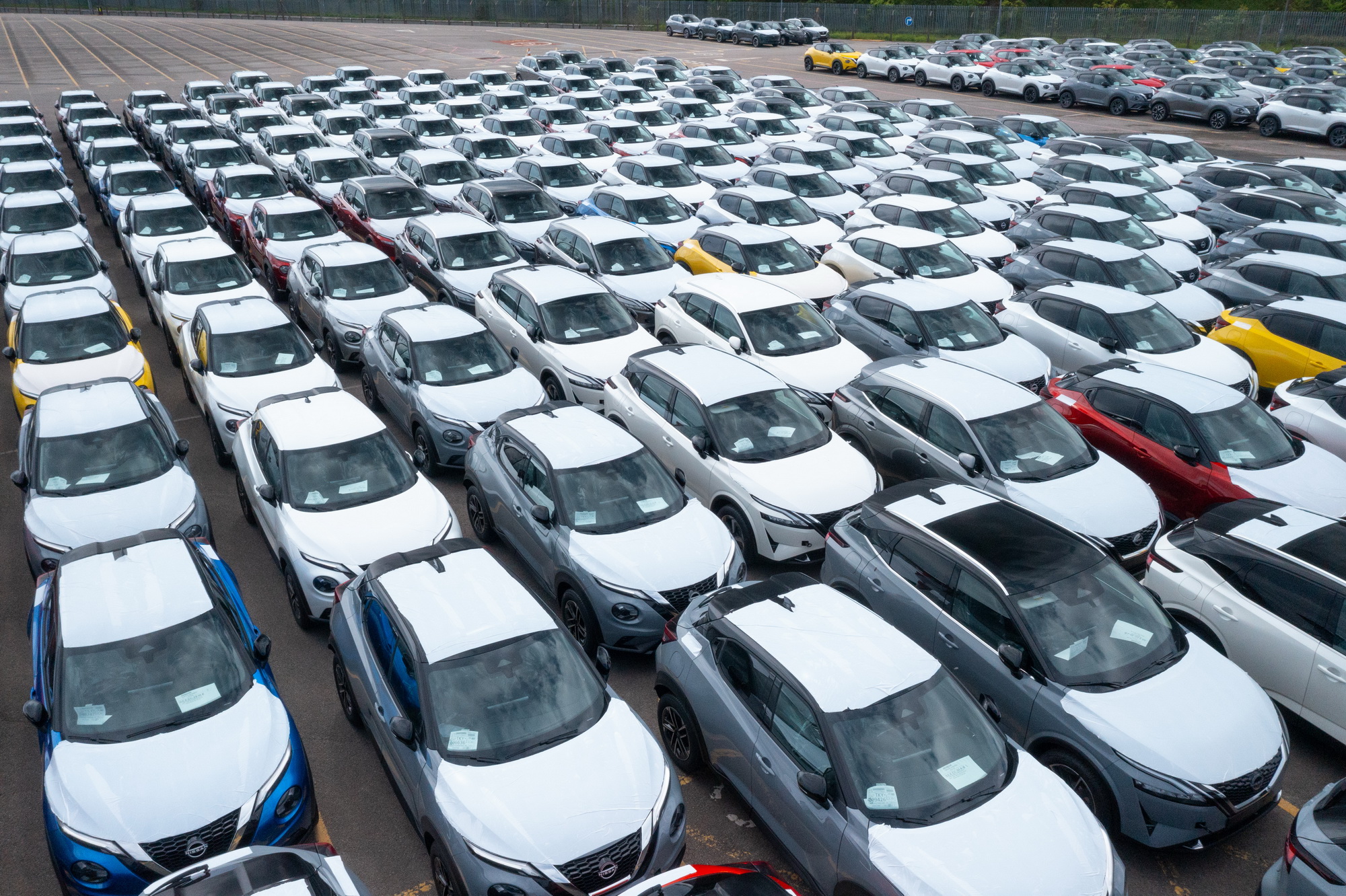
Βάζοντας τα πράγματα σε μια σειρά, θα ξεκινήσουμε λέγοντας ότι το εργοστάσιο της Nissan αποτελεί κομμάτι μια επένδυσης της εταιρίας στο Ηνωμένο Βασίλειο που ξεπερνά τα έξι δισεκατομμύρια στερλίνες. Ως κομμάτι του οικοσυστήματος της εταιρίας στο «Εργοστάσιο του Κόσμου» (σ.σ. έκφραση που προσδιορίζει την πάλαι ποτέ Μεγάλη Βρετανία), το εργοστάσιο της Nissan λειτουργεί ήδη από το 1986, οπότε και το Nissan Bluebird εγκαινίασε τη γραμμή παραγωγής.
Από το 2006 στη μονάδα του Sunderland κατασκευάζεται το Qashqai, εξ ολοκλήρου σχεδιασμένο και κατασκευασμένο στη Βρετανία. Και μέχρι σήμερα έχουν αφήσει πίσω τους το εργοστάσιο πάνω από 4.000.000 μονάδες με προορισμό περισσότερες από 100 χώρες παγκοσμίως.
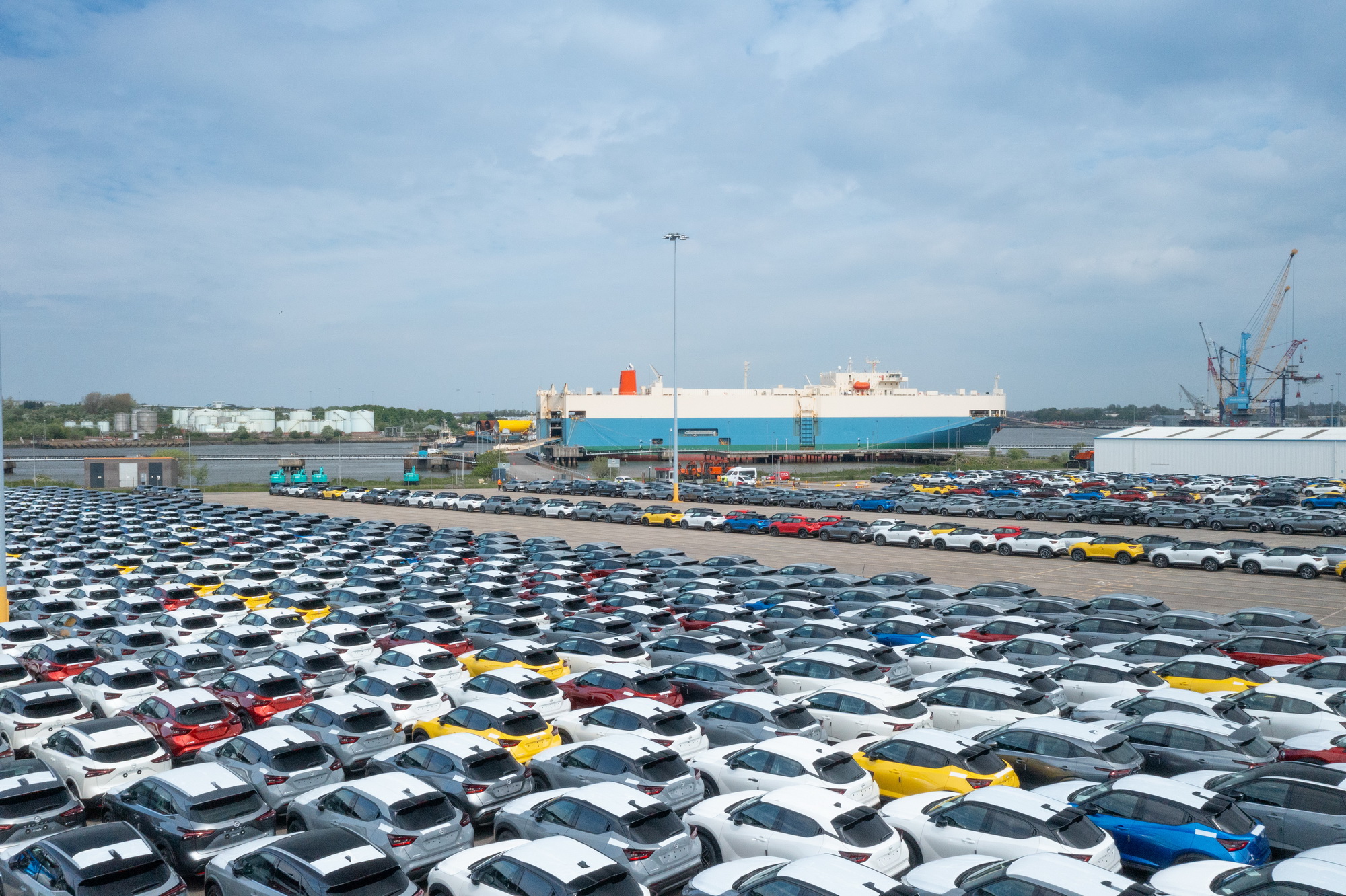
Αν κάποιος κάνει την πράξη, θα αντιληφθεί ότι κάθε δυο λεπτά για τα τελευταία 18 χρόνια, ένα Qashqai βγαίνει από την γραμμή παραγωγής. Θα μπορούσε λοιπόν κάποιος να χαρακτηρίσει την παραγωγή του ακόμα και ως επιτυχημένη! Η έναρξη της κατασκευής για την τελευταία γενιά του ιαπωνικού SUV συνοδεύθηκε από μία επιπλέον επένδυση 30 εκατομμυρίων στερλινών, Επένδυση, προκειμένου η γραμμή παραγωγής να τροποποιηθεί για τις ανάγκες του ανανεωμένου μοντέλου, αλλά και να μπει σε τροχιά σύμφωνη με το πλάνο της εταιρίας για το εργοστάσιο «EV360».
Πλησιάζοντας το εργοστάσιο το πρώτο πράγμα που παρατηρείς είναι οι δέκα ανεμογεννήτριες. Σε συνδυασμό δε με τα 19.000 φωτοβολταϊκά πάνελ μπορούν να παράγουν περισσότερο από το 20% της απαιτούμενης ενέργειας, συμβάλλοντας στη βιωσιμότητα της παραγωγής. Όπως ανέφερε και η Friederike Kienitz (Senior Vice President, Sustainability, Corporate Governance, Legal, External Affairs and Communications, AMIEO Region) ένας από τους κεντρικούς πυλώνες του σχεδίου «EV360» είναι η παραγωγή της απαιτούμενης ενέργειας από 100% ίδιες, ανανεώσιμες πηγές ενέργειας.
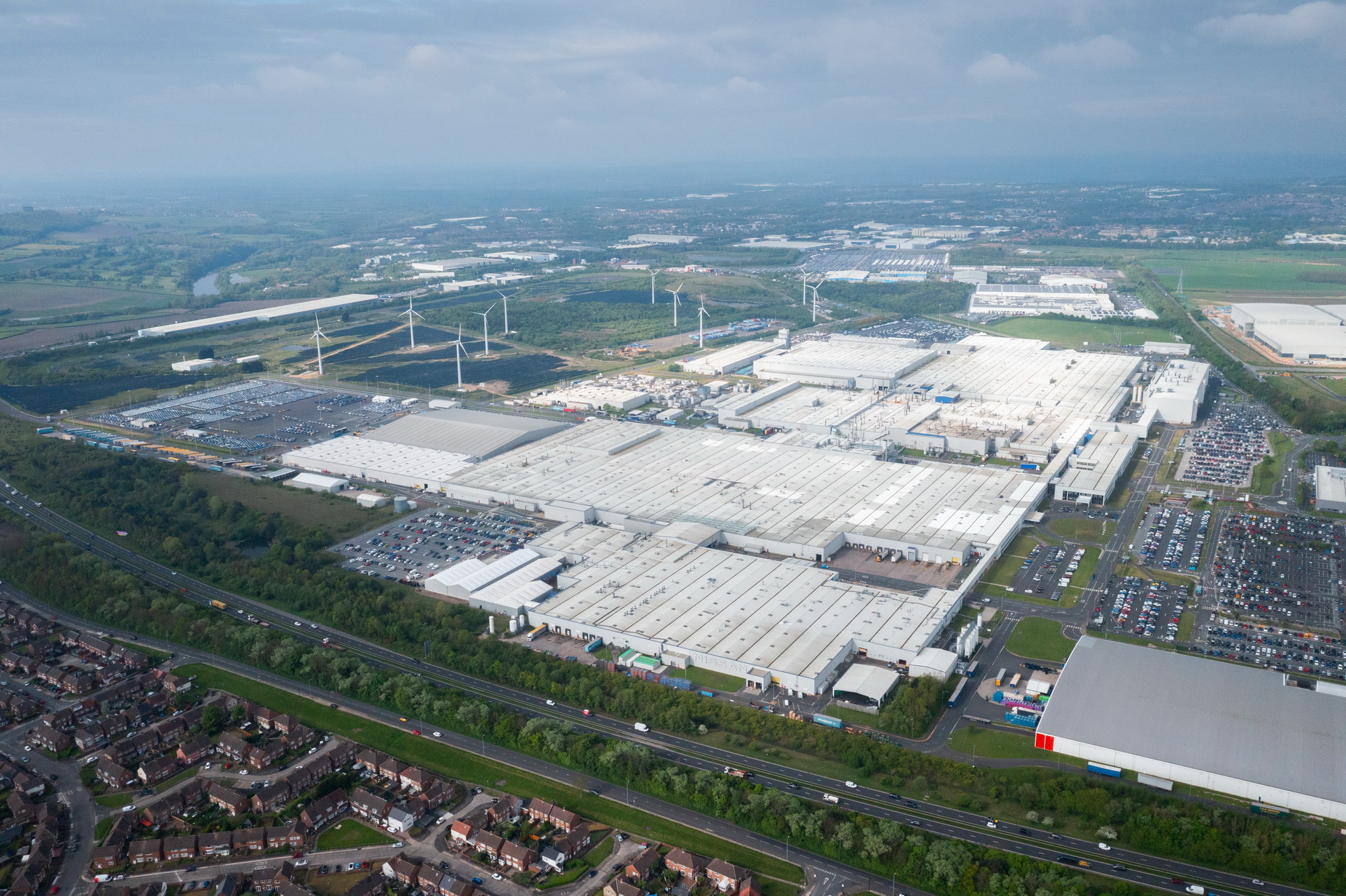
Το παραπάνω, σε συνδυασμό με το μοντέλο του microgrid, όχι μόνο θα μειώσει το αποτύπωμα του εργοστασίου σε άνθρακα, αλλά και θα αποδεσμεύσει το ήδη βεβαρυμμένο δίκτυο μεταφοράς ενέργειας της Βρετανίας. Βλέπετε, η ενέργεια θα παράγεται και θα μεταφέρεται on site, με χρήση εσωτερικού δικτύου.
Στη δε αποθήκευση του ενεργειακού πλεονάσματος, θα συμβάλλουν ανακυκλωμένες μπαταρίες ηλεκτρικών και υβριδικών αυτοκινήτων της εταιρείας που, όπως ανέφερε η Kienitz, μπορεί να μην έχουν ικανοποιητική απόδοση για οδική χρήση, αλλά αποτελούν εξαιρετική επιλογή αποθηκών ενέργειας.
Η Nissan έχοντας χρόνια εμπειρίας σε υβριδικά μοντέλα, είναι σε θέση να προσεγγίσει τον νέο αυτόν τομέα αποθήκευσης ενέργειας, ως ένα πολλά υποσχόμενο επιχειρηματικό πλάνο. Αντιμετωπίζοντας ταυτόχρονα το επικείμενο πρόβλημα ανακύκλωσης των μπαταριών υβριδικών και ηλεκτρικών αυτοκινήτων που φτάνουν πλέον στο τέλος της χρήσης τους στο πλαίσιο της αυτοκίνησης.
Προκειμένου να παρακολουθείται και να διασφαλίζεται η ενεργειακή αποδοτικότητα, έχουν εγκατασταθεί περισσότεροι από 230 έξυπνοι μετρητές στις εγκαταστάσεις. Η ειδικά σχεδιασμένη ψηφιακή υποδομή της μονάδας καθιστά εφικτή τη δημιουργία αναφορών σε πραγματικό χρόνο, που αφορούν την κατανάλωση ενέργειας και την εποπτεία των διαφόρων σταδίων παραγωγής. Επιτρέποντας έτσι τη διασφάλιση της απρόσκοπτης παραγωγικής διαδικασίας.
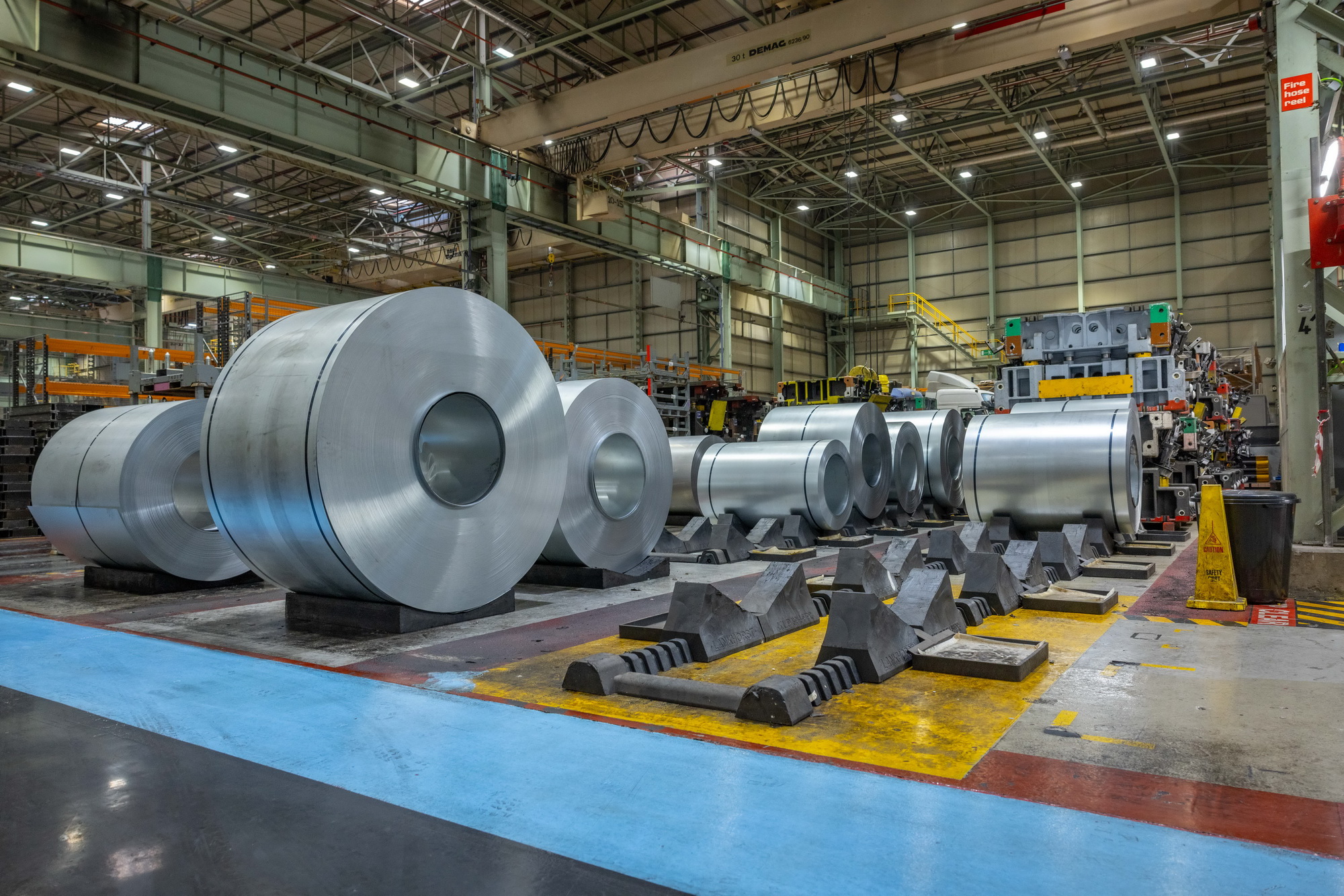
Πρώτο στάδιο της διαδικασίας είναι η μορφοποίηση και κατασκευή των επιφανειών που απαρτίζουν το αμάξωμα του αυτοκινήτου. Κατά την επίσκεψη μας βρεθήκαμε στη μεγαλύτερη από τις «πρέσες» που διαθέτει το εργοστάσιο στο αποκαλούμενο «Press Shop». Η αρχική μορφή του κάθε πάνελ είναι ένα ογκώδες ρολό χάλυβα ή αλουμινίου. Αυτό το δεύτερο, χρησιμοποιούμενο σε επιλεγμένα κομμάτια του πλαισίου επιτρέπει την εξοικονόμηση 60 kg από το αμάξωμα και κατ’ επέκταση εξοικονομεί καύσιμα κατά τη χρήση του αυτοκινήτου.
Όλα τα πάνελ φτάνουν στο στάδιο επεξεργασίας «Just-in-Time», εξασφαλίζοντας τη μέγιστη εξοικονόμηση χώρου. Με το συνολικό απόθεμα που διατηρείται στις εγκαταστάσεις να διαρκεί για μόλις μερικές ώρες παραγωγής. Με πίεση που ξεπερνά του 7.000 τόνους, τα φύλλα αλουμινίου μετατρέπονται στα γνώριμα μέρη ενός αυτοκινήτου. Με το περισσευούμενο υλικό να απορροφάται από ένα ισχυρό σύστημα αναρρόφησης, προκειμένου να επαναχρησιμοποιηθεί στην παραγωγή αλουμινίου.
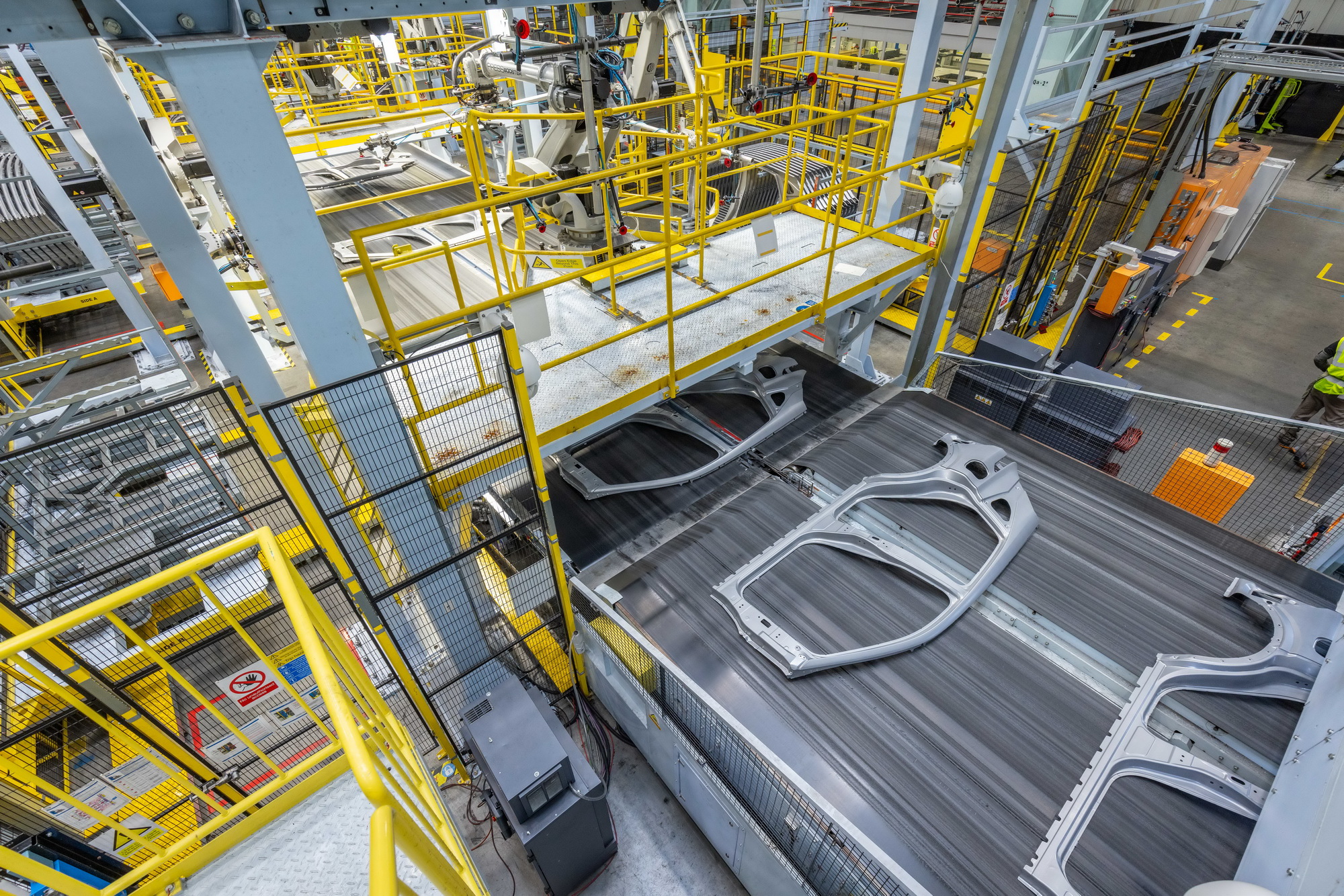
Σύμφωνα με τα δεδομένα της Nissan, η ανακύκλωση αλουμινίου μπορεί να εξοικονομήσει έως και 90% της ενέργειας που απαιτείται στο χυτήριο. Δεν θα γινόταν άλλωστε, ένα εργοστάσιο που θέλει να χαρακτηρίζεται ως «βιώσιμο» να απορρίπτει όλη αυτήν την ποσότητα χρήσιμου υλικού.
Με τη δημιουργία των πάνελ εμφανίζεται και η πρώτη ανθρώπινη επέμβαση στη διαδικασία παραγωγής.
Το Sunderland δεν επιλέχθηκε τυχαία, άλλωστε, από τη Nissan. Εκτός από την στρατηγική θέση του δίπλα σε λιμάνι, διαθέτει και μακρά παράδοση στη ναυπηγεία, δημιουργώντας μια πληθώρα έμπειρων τεχνικών που αναζητούν τυχόν ατέλειες προτού επιτρέψουν στο εκάστοτε κομμάτι να προχωρήσει παραπέρα στη συναρμολόγηση και στη βαφή.
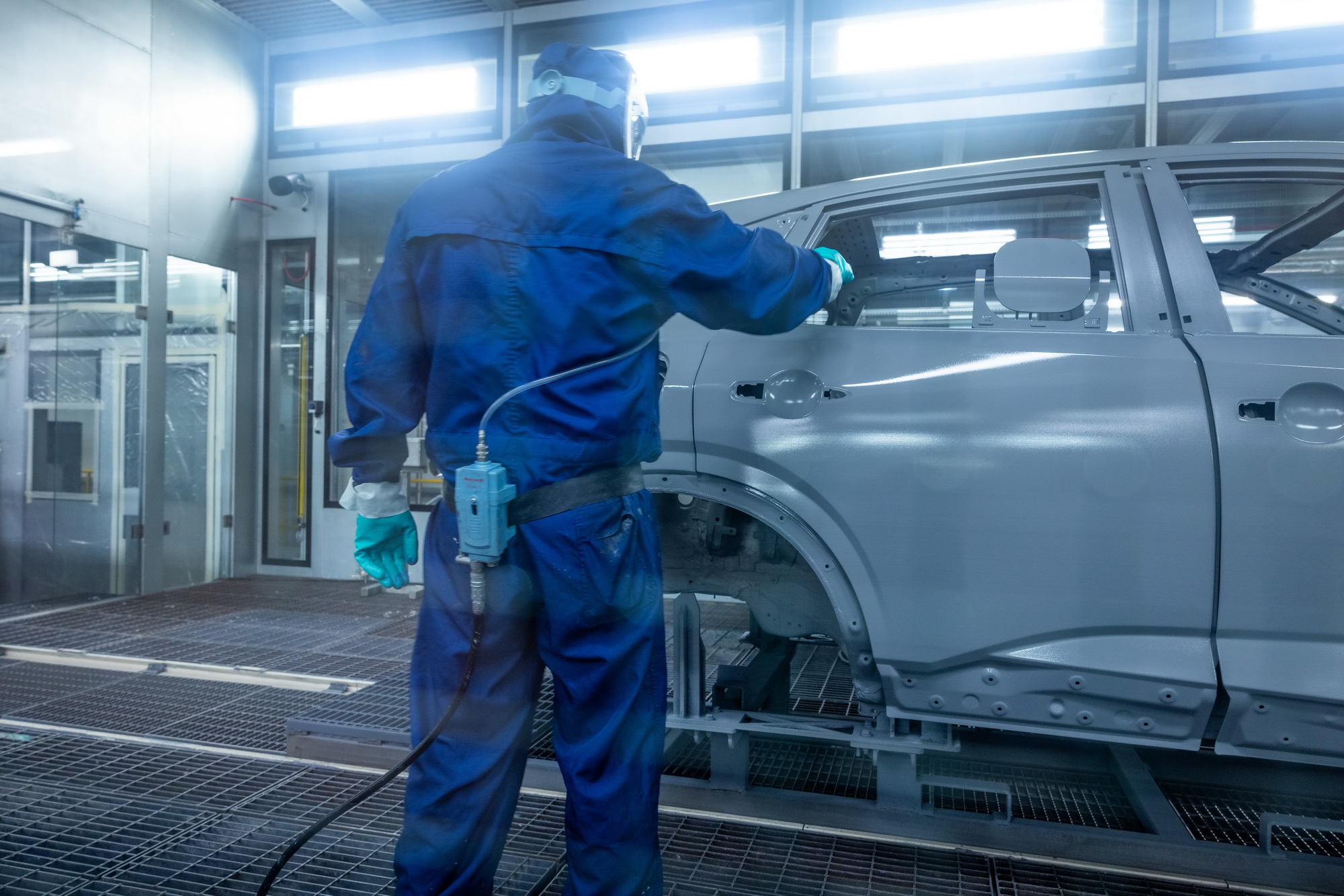
Όπως σημείωσε ο Alan Johnson (Senior Vice President, Region Manufacturing & Supply Chain), ο ανθρώπινος παράγοντας είναι στρατηγικά ενσωματωμένος στην παραγωγή, σε σημεία μάλιστα όπου άλλοι κατασκευαστές επιλέγουν την αυτοματοποίηση. «Μπορεί να είναι εντυπωσιακό από τεχνολογικής άποψης, αλλά ανούσιο από επιχειρηματικής», σημείωσε χαρακτηριστικά, τονίζοντας την εμπιστοσύνη που δείχνει η Nissan στην ικανότητα και στην ταχύτητα των εργαζομένων της.
Μάλιστα, συνέχισε, η φιλοσοφία του ιαπωνικού κολοσσού είναι να μεριμνά για την ευημερία των υπαλλήλων του. Χαρακτηριστικό παράδειγμα είναι η προσπάθεια προσαρμογής των ωραρίων των βαρδιών στο εργοστάσιο στις ανάγκες τους. Στόχος είναι να μπορεί να ο εργαζόμενος να επιλέγει λ.χ. μόνο πρωινές βάρδιες, διότι αυτό τον βολεύει και να μη χρειάζεται να αντιμετωπίζει ένα κυλιόμενο ωράριο.
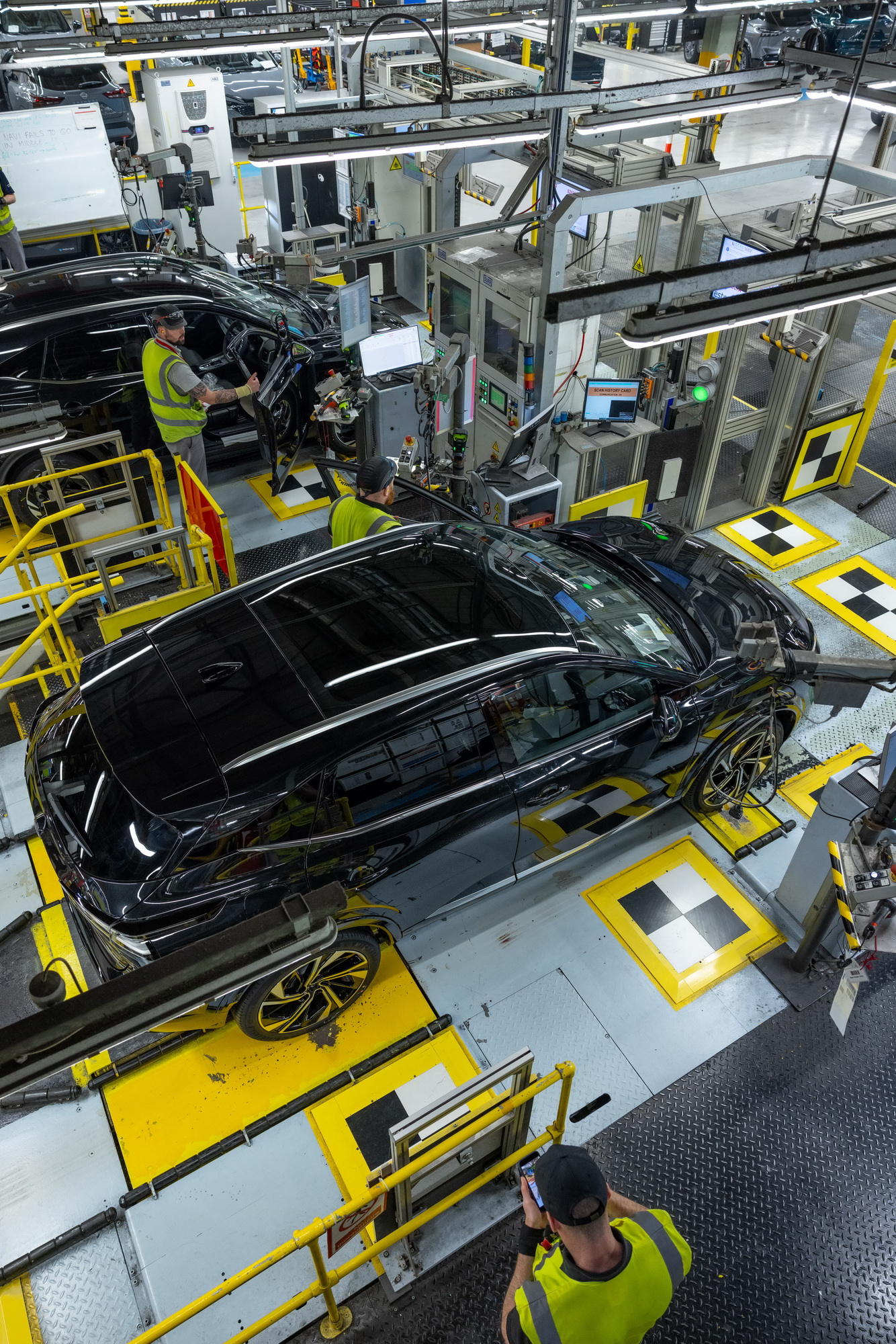
Ένα μικρό βήμα αλλά όχι ανούσιο βήμα προς την κατεύθυνση αυτή είναι η αναπαραγωγή μουσικής από τα μεγάφωνο του χώρου τελικής συναρμολόγησης των αυτοκινήτων, Trim and Chassis, προκειμένου να γίνεται πιο ευχάριστη η ήδη απαιτητική εργασία!
Σε αυτό το σημείο μας έκανε πραγματικά εντύπωση η ευρηματικότητα των μηχανικών παραγωγής. Ο δεύτερος πυλώνας της στρατηγικής «EV36Zero» είναι η παραγωγή στο εργοστάσιο τριών νέων αμιγώς ηλεκτρικών αυτοκινήτων, καθώς και αμιγώς ηλεκτρικών εκδόσεων των Qashqai και Juke. Η εταιρία θέλει μάλιστα, μέχρι το τέλος του 2026, να έχει 46% ηλεκτρική παρουσία στην αγορά της Γηραιάς Ηπείρου.
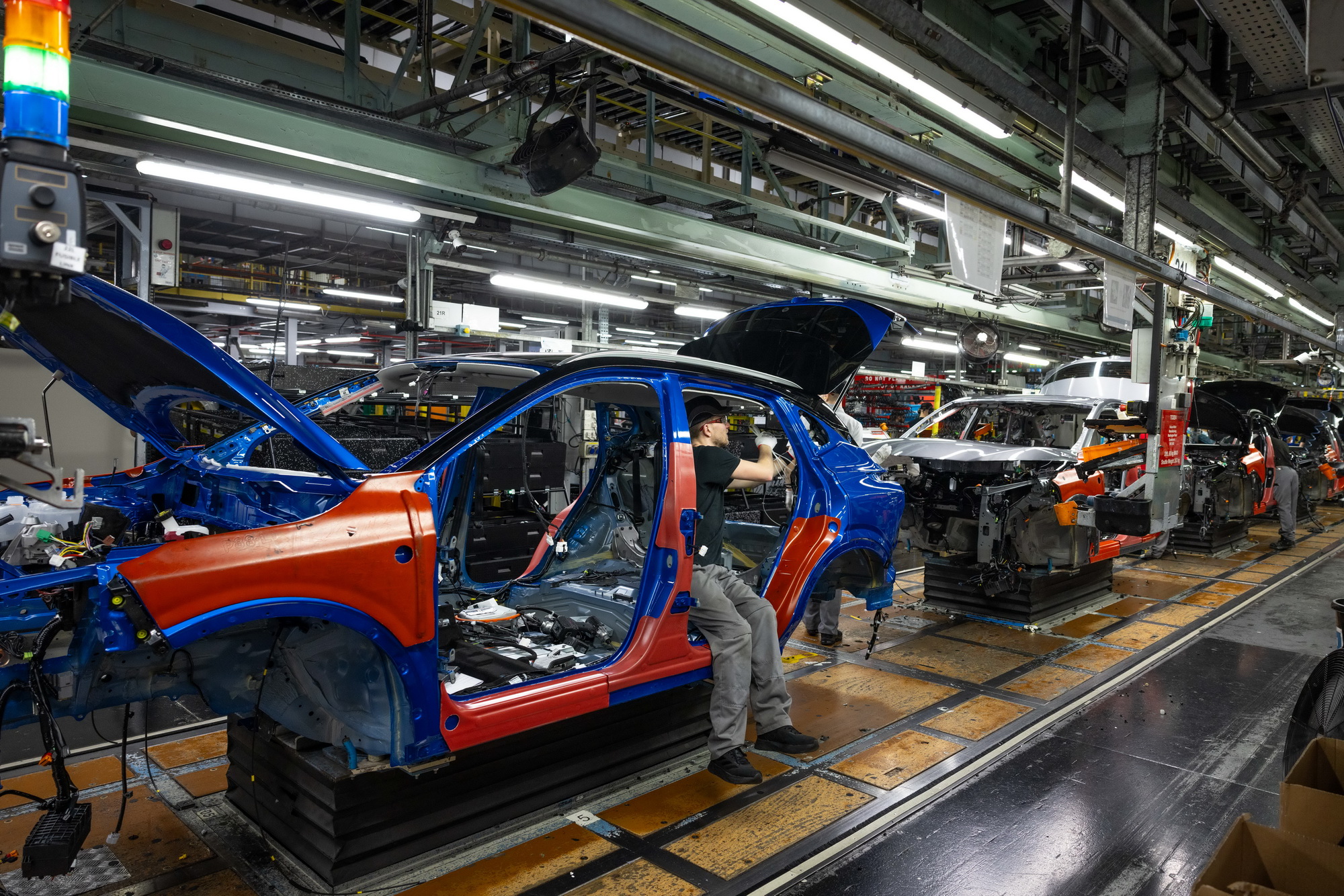
Προκειμένου να επιτευχθεί αυτό χρειαζόταν η ενσωμάτωση υποδομής για την τοποθέτηση μεγαλύτερων μπαταριών στην ήδη υπάρχουσα γραμμή παραγωγής. Μάλιστα, καθώς η φιλοσοφία παραγωγής είναι αυτή του «on-demand», δηλαδή τα αυτοκίνητα δεν παράγονται σε ομάδες με κοινά χαρακτηριστικά, αλλά εισάγονται στη γραμμή παραγωγής όπως διαμορφώνονται οι παραγγελίες, έπρεπε να διατηρηθεί και η υπάρχουσα ευελιξία παραγωγής.
Η λύση ήταν ιδιοφυώς απλή –«απλή» για τον παρατηρητή. Αφού έχει συναρμολογηθεί και το εσωτερικό του αυτοκινήτου και πριν γίνει η ζεύξη του αμαξώματος με το σύστημα κίνησης, μια πλατφόρμα που τοποθετήθηκε κάτω από την ήδη υπάρχουσα κυλιόμενη εγκατάσταση μεταφοράς των αμαξωμάτων, αναλαμβάνει την ανύψωση, εφαρμογή και τοποθέτηση της μπαταρίας. Και η γραμμή παραγωγής μόλις απέκτησε και 100% ηλεκτρικό χαρακτήρα!
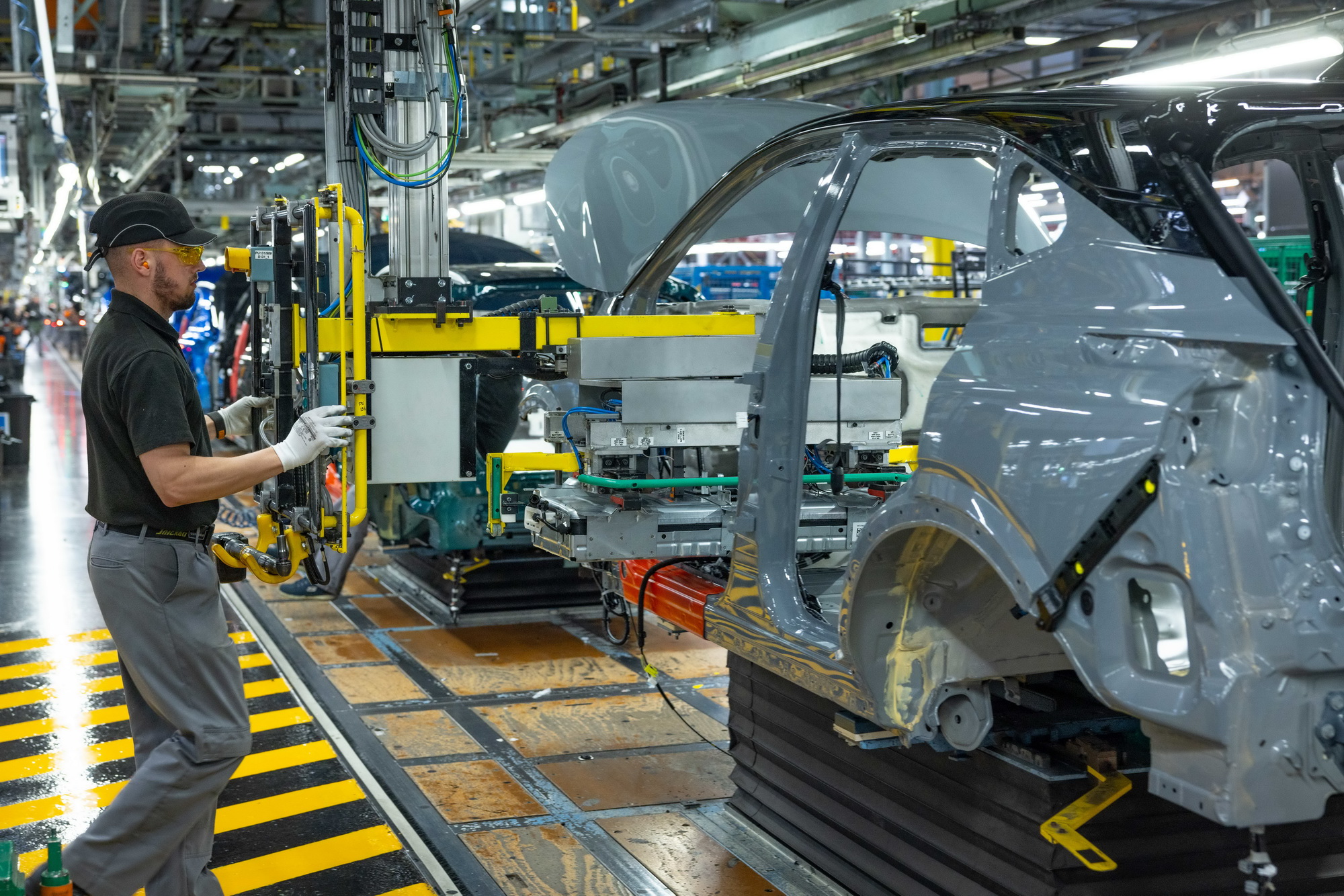
Φυσικά, μια αποτελεσματική γραμμή παραγωγής δεν θα ήταν δυνατή χωρίς την αρμονική συνύπαρξη μηχανών και ανθρωπίνου δυναμικού. Διότι μπορεί η Nissan να εμπιστεύεται τους τεχνικούς της για να πραγματοποιούν τις όποιες εργασίες (πέραν της συγκόλλησης και της βαφής που γίνεται από αυτοματοποιημένα μηχανήματα), χρησιμοποιεί όμως και αυτόνομα οχήματα. AV που μεταφέρουν τα υλικά ή και ολόκληρα στελέχη του τελικού αυτοκινήτου εκεί που πρέπει να βρίσκονται, εγκαίρως και χωρίς να δημιουργούν συμφόρηση στους χώρους της μονάδας.
Όλη η ροή των υλικών από το «Press Shop», στο «Body Shop», έπειτα στο «Paint Shop» και τέλος στο «Trim and Chassis» είναι αδιάλειπτη και απρόσκοπτη, ακολουθώντας μια κυκλική πορεία εντός του εργοστασίου. Επιπλέον έξυπνα συστήματα καθοδηγούν του τεχνικούς και διασφαλίζουν τη σωστή αλληλουχία βημάτων και την ποιότητα συναρμογής.
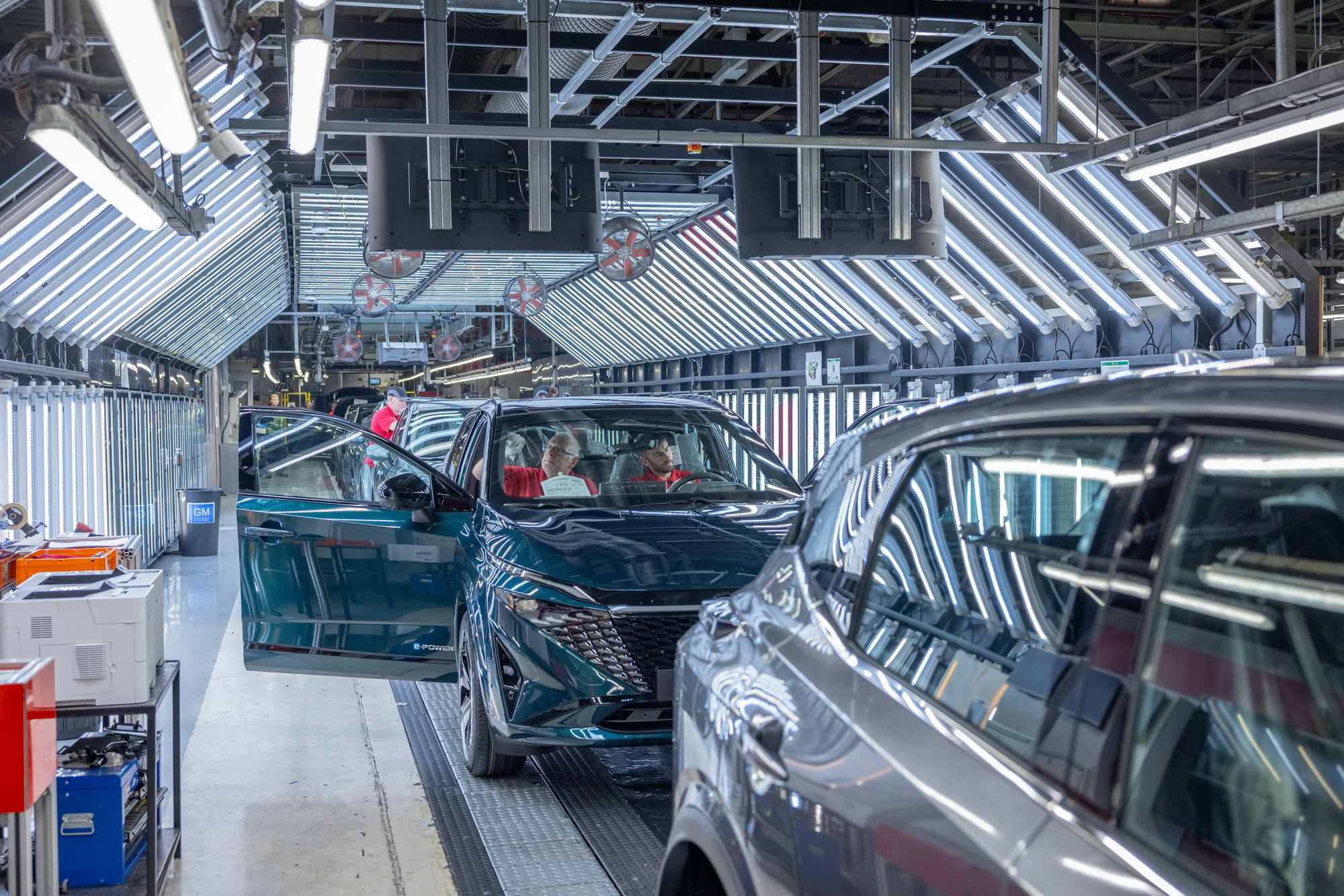
Είχαμε την ευκαιρία να βιώσουμε το παραπάνω στην πράξη, καθώς οι άνθρωποι του εργοστασίου μας «εμπιστεύθηκαν» να συναρμολογήσουμε μια μπαταρία -φυσικά αποφορτισμένη.
Το αυτόματο μπουλονόκλειδο σε συνδυασμό με δύο κάμερες εξασφάλισε ότι, ακόμα κι εμείς, θα σφίγγαμε τα παξιμάδια στη σωστή προδιαγραφή ροπής και με τη σωστή σειρά. Εάν κάποιο κομμάτι δεν ολοκληρωνόταν ορθά, το εργαλείο έμπαινε αυτόματα σε λειτουργία αποσυναρμολόγησης, έτσι ώστε να επαναληφθεί το βήμα. Ή απενεργοποιείτο ώστε να αποτρέψει λάθος ενέργεια.
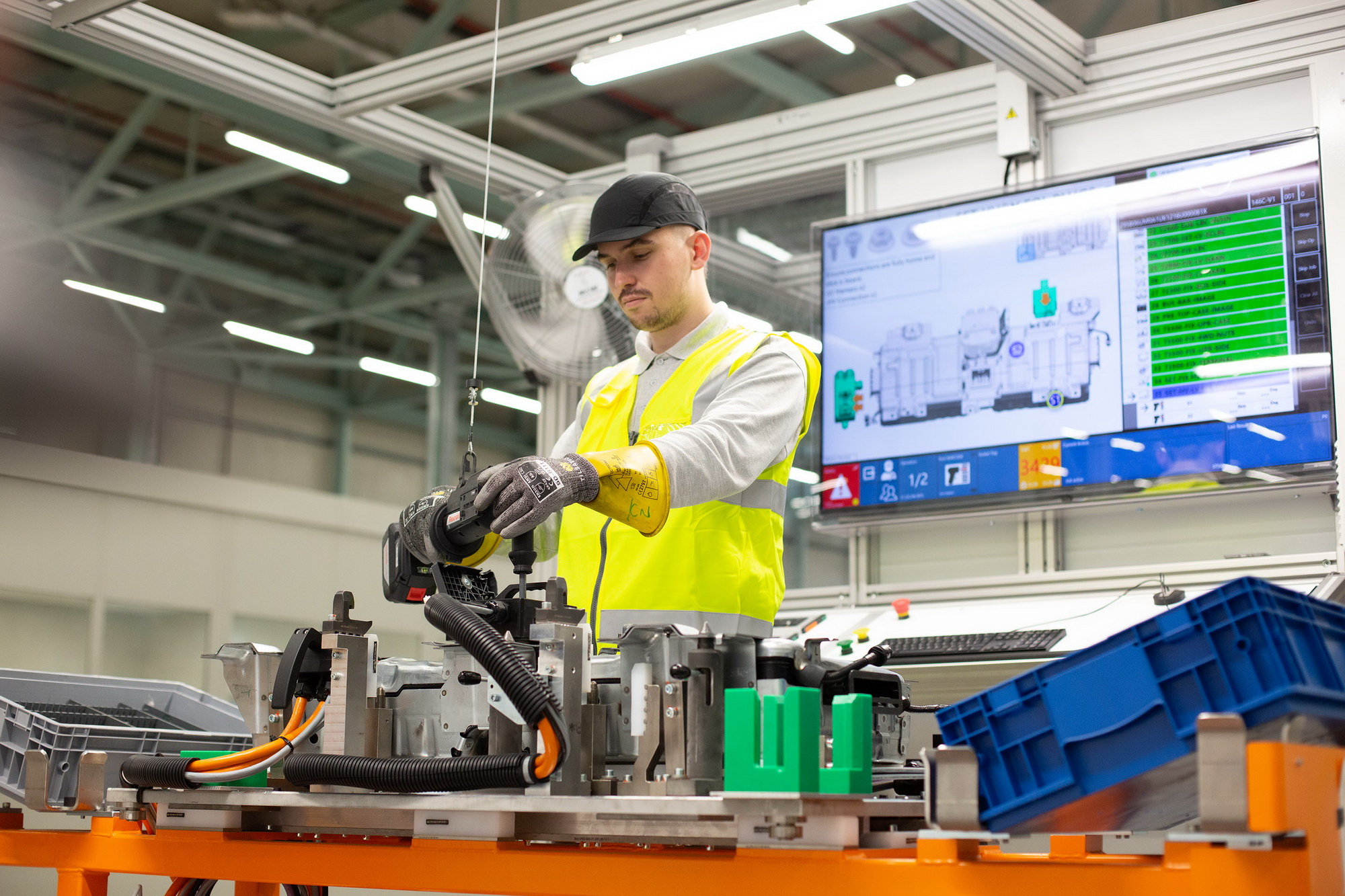
Θα μπορούσε κάποιος να υποθέσει ότι η συγκεκριμένη εργασία είναι επομένως εύκολη, οι άνθρωποι της Nissan όμως μας επιφύλασσαν μια έκπληξη. Με το πέρας της επίσκεψής μας στους χώρους του εργοστασίου, γνωρίσαμε το πρώτο βήμα στο στάδιο αξιολόγησης μελλοντικών εργαζομένων. Το ζητούμενο ακούγεται απλό: Ολοκλήρωση πέντε βασικών εργασιών, όπως βίδωμα και συναρμογή υλικών.
Το εντυπωσιακό έγκειται στο γεγονός ότι ένας υποψήφιος πρέπει να ολοκληρώσει των κύκλων εργασιών 16 φορές εντός δέκα λεπτών. Με ταυτόχρονη απαίτηση να κινείται σε στενά μέρη περιφερειακά και εντός του αμαξώματος. Απαιτείται δηλαδή μέγιστος χρόνος περίπου μισού λεπτού ανά κύκλο. Προς σύγκριση αρκεί κάποιος να προσπαθήσει να στερεώσει μία βίδα με δύο washers και παξιμάδι, τοποθετημένα στη σωστή σειρά, ανά 4 δευτερόλεπτα, με σταθερό ρυθμό!
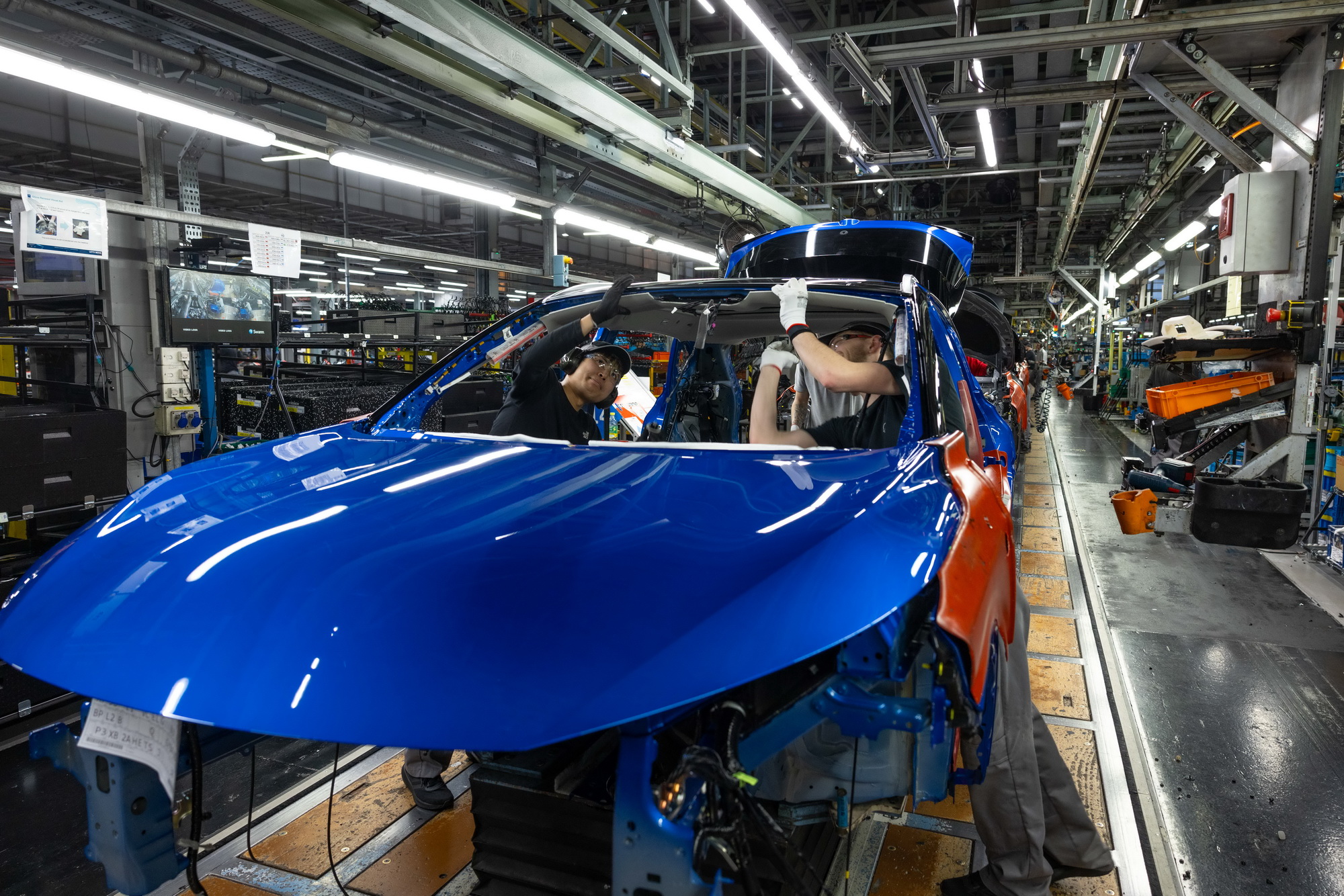
Σε ερώτηση που έγινε στους υπεύθυνους αξιολόγησης, τονίσανε ότι οι εργαζόμενοι αλλάζουν συχνά θέσεις εργασίας, προκειμένου να αποφευχθεί τυχόν τραυματισμός από τη διαρκώς επαναλαμβανόμενη κίνηση.
Ολοκληρώνοντας την επίσκεψη μας στο εργοστάσιο παραγωγής της Nissan στο Sunderland, δηλώνουμε εντυπωσιασμένοι. Πρωτίστως, διότι είχαμε την ευκαιρία να δούμε στην πράξη πώς μετουσιώνεται το καθημερινό μας αυτοκίνητο, συνδυάζοντας πολλές χιλιάδες κομμάτια. Με τη συνολική διαδικασία παραγωγής ενός ολοκληρωμένου αυτοκινήτου, έτοιμου για τελικό έλεγχο, να διαρκεί μόλις 14 ώρες!
Κυρίως όμως, παρακολουθήσαμε πώς επιτυγχάνεται η αρμονική συνεργασία μηχανημάτων και ανθρώπων, ολοκληρώνοντας μια αποτελεσματική και απρόσκοπτη παραγωγική αλυσίδα στα πλαίσια του μοντέλου ενός πραγματικού «Gigafactory».